The size and capacity of a block making machine significantly impact its production output.
Here’s how these factors are interconnected:
1. Size of the Machine:
- Size of Molds: The size of the machine, particularly the size of the molds it can accommodate, determines the maximum dimensions of the blocks or bricks that can be produced. Larger machines with bigger molds can make larger blocks.
- Footprint: The physical size of the machine affects its installation and workspace requirements. Smaller machines are more compact and require less space.
- Mobility: Smaller machines are often more portable and can be easily transported to construction sites or different locations. Larger machines are typically stationary.
2. Capacity of the Machine:
- Production Rate: The capacity of the machine, often measured in terms of blocks or bricks produced per hour, determines its production rate. Higher-capacity machines can produce more units in a given time frame.
- Batch Size: Some block making machines operate in batch mode, where a certain number of blocks are produced in each cycle. The batch size affects the production rate and can vary with machine capacity.
- Automation Level: Machines with higher capacity often feature more automation, which can increase efficiency and productivity. They may have automated feeding systems, block ejection, and stacking mechanisms.
3. Impact on Production Output:
- Higher Capacity, Increased Output: Generally, larger machines with greater capacity can produce a higher volume of blocks or bricks in a given time. This is especially important for large construction projects that require a substantial number of building units.
- Efficiency and Consistency: Larger machines may offer better efficiency and consistency in production due to their automated features and larger production cycles.
- Variety of Products: Smaller machines are suitable for small-scale projects and may be versatile in producing various block sizes and shapes. Larger machines are often more specialized and optimized for high-volume production of specific block sizes.
- Resource Requirements: Larger machines may require more raw materials, such as concrete or clay, to meet their capacity. This should be factored into production planning.
It’s important to choose a block making machine that aligns with the specific needs of a construction project. The size and capacity should be selected based on the required block dimensions, the production rate, block making machine china available workspace, and available resources. Smaller, more versatile machines are suitable for smaller projects or when flexibility in block sizes is needed. Larger, high-capacity machines are better suited for large-scale construction projects that demand a high volume of uniform blocks or bricks.
What types of blocks or bricks can be produced using a block making machine?
Block making machines are versatile tools that can produce a variety of blocks and bricks, depending on the design of the machine and the type of molds or dies used. Common types of blocks and bricks that can be produced using a block making machine include:
- Solid Blocks: These are dense, solid blocks used for load-bearing walls and various structural applications. They have no voids or cavities and offer excellent compressive strength.
- Hollow Blocks: Hollow blocks have one or more voids or cavities, which reduce their weight and material usage. They are commonly used in construction for both load-bearing and non-load-bearing walls. Hollow blocks can provide insulation against heat and sound.
- Interlocking Blocks: These blocks have unique designs that allow them to interlock or fit together without the need for mortar or adhesives. Interlocking blocks are popular for applications like retaining walls and erosion control.
- Paving Blocks: Also known as pavers or paving stones, these are used to create decorative and functional paved surfaces, such as walkways, driveways, and patios. Paving blocks come in various shapes, sizes, and patterns.
- Cinder Blocks: Cinder blocks, also called concrete masonry units (CMUs), are rectangular or square blocks with hollow cavities. They are used in various construction applications, including walls, partitions, and foundations.
- Fly Ash Bricks: These are environmentally friendly bricks made from a mixture of fly ash, cement, and other materials. They are known for their strength and thermal insulation properties.
- Perforated Blocks: These blocks have small holes or perforations, often used for ventilation and decorative purposes. They can also reduce the weight of the block.
- Specialty Blocks: Some block making machines are designed to produce specialty blocks with unique shapes or features, such as wave blocks, slope blocks, or corner blocks.
- Split Face Blocks: These blocks have a rough, textured surface and are often used for decorative or architectural purposes, providing an aesthetically pleasing appearance.
- Conventional Bricks: Some block making machines can produce traditional clay or concrete bricks, which are used in a wide range of construction applications.
The choice of the type of block or brick to produce depends on the intended use, design requirements, and construction project specifications. Block making machines offer the flexibility to adapt to various construction needs, making them valuable tools in the construction industry.
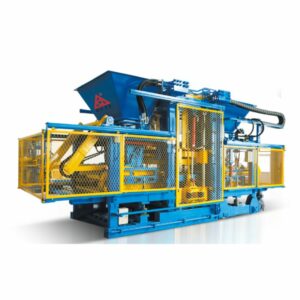