The design of the track chain in heavy machinery such as excavators significantly impacts the overall reliability and uptime of the machine. Here’s how:
- Material Selection: The track chain is typically constructed from high-strength materials such as alloy steel or manganese steel. These materials are chosen for their durability, wear resistance, and ability to withstand heavy loads and harsh operating conditions. A well-designed track chain made from quality materials can withstand continuous use without premature failure, contributing to the reliability of the machine.
- Heat Treatment: Many track chains undergo heat treatment processes such as quenching and tempering to enhance their mechanical properties, including hardness, toughness, and fatigue resistance. Proper heat treatment improves the strength and durability of the track chain, reducing the risk of breakage or deformation during operation and increasing overall reliability.
- Link Design: The design of the track chain links influences their ability to withstand stress and wear. Robust link designs with reinforced sections, hardened surfaces, and proper geometry distribute loads more effectively, reducing the risk of stress concentrations and premature wear. Additionally, self-cleaning features in the link design help prevent the accumulation of debris and contaminants that could accelerate wear and reduce reliability.
- Sealing and Lubrication: Effective sealing and lubrication systems are essential for maintaining the performance and longevity of the track chain. Sealed and lubricated track chains reduce friction, wear, and corrosion, extending the service life of the components and minimizing the risk of premature failure. Proper lubrication also helps dissipate heat generated during operation, reducing thermal stress on the track chain.
- Track Tensioning System: The track chain is tensioned to ensure proper engagement with the sprockets and idlers, preventing slippage and derailment. Well-designed track tensioning systems, such as hydraulic or spring tensioners, maintain optimal track tension throughout the operating range, enhancing reliability and reducing downtime associated with track adjustments or replacements.
- Resistance to Wear and Deformation: The track chain is subjected to continuous wear and deformation during operation, particularly in abrasive or high-impact environments. A durable track chain design with hardened surfaces, wear-resistant materials, and proper heat treatment resists wear and deformation, maintaining dimensional stability and reliability over time.
- Compatibility with Undercarriage Components: The design of the track chain must be compatible with other undercarriage components such as rollers, idlers, and sprockets to ensure smooth and efficient operation. Proper alignment, clearance, and engagement between the track chain and undercarriage components minimize stress, wear, and premature failure, maximizing overall reliability and uptime.
Overall, the design of the track chain plays a critical role in the reliability and uptime of heavy machinery like excavators. By incorporating high-quality materials, robust link designs, effective sealing and lubrication systems, proper track tensioning, resistance to wear and deformation, and compatibility with undercarriage components, a well-designed track chain enhances the durability, performance, and longevity of the machine, ultimately reducing downtime and maintenance costs.
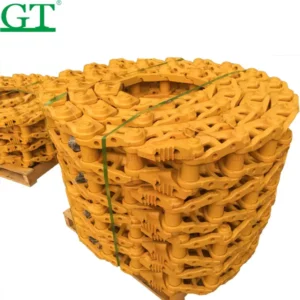