Excavator undercarriages are designed to adapt to different ground conditions and surface types, offering versatility and performance in various environments.
Here’s how they achieve adaptability:
- Track Design: Excavator undercarriages feature tracks with different designs tailored to specific ground conditions. For example, excavators used in muddy or swampy terrain may have wider tracks with larger surface areas to distribute weight and prevent sinking. Conversely, excavators used on rocky terrain may have narrower tracks with reinforced construction to withstand impact and abrasion.
- Track Shoes: The type of track shoes used on excavators can vary depending on the ground conditions. Rubberized or polyurethane-coated track shoes are suitable for surfaces that require minimal ground disturbance, such as paved surfaces or delicate landscapes. Steel track shoes with aggressive treads are ideal for challenging terrain, providing superior traction and grip on loose or uneven surfaces.
- Track Tensioning: Excavator undercarriages are equipped with track tensioning systems that allow operators to adjust the tension of the tracks to suit different ground conditions. Proper track tensioning ensures optimal track performance, minimizing track slippage and excessive wear, regardless of the surface type.
- Undercarriage Components: The components of the excavator undercarriage, including track rollers, idlers, and sprockets, are designed to withstand the rigors of various ground conditions. excavator undercarriage Heavy-duty components with sealed bearings and reinforced construction provide durability and reliability in challenging environments, ensuring smooth operation and minimal downtime.
- Ground Clearance: Excavator undercarriages are configured to provide adequate ground clearance to navigate obstacles and uneven terrain. High-clearance designs prevent the undercarriage from getting caught on rocks, roots, or debris, allowing the excavator to traverse rough terrain with minimal disruption.
- Ground Pressure: Excavator undercarriages are engineered to distribute the weight of the machine evenly across the tracks, reducing ground pressure and minimizing soil compaction. This helps preserve the integrity of delicate surfaces such as turf or landscaping while providing sufficient traction and stability for the excavator to operate effectively.
- Track Width Adjustment: Some excavators feature adjustable track widths that allow operators to modify the width of the tracks to suit specific ground conditions. Narrower track widths are advantageous for maneuvering in confined spaces or on narrow trails, while wider track widths provide enhanced stability and flotation on soft or unstable terrain.
Overall, excavator undercarriages are designed with adaptability in mind, offering flexibility, durability, and performance in a wide range of ground conditions and surface types. By incorporating features such as diverse track designs, adjustable track tensioning systems, heavy-duty components, adequate ground clearance, optimized ground pressure, and track width adjustment capabilities, excavator undercarriages can effectively navigate diverse environments and deliver reliable performance in various construction, landscaping, and earthmoving applications.
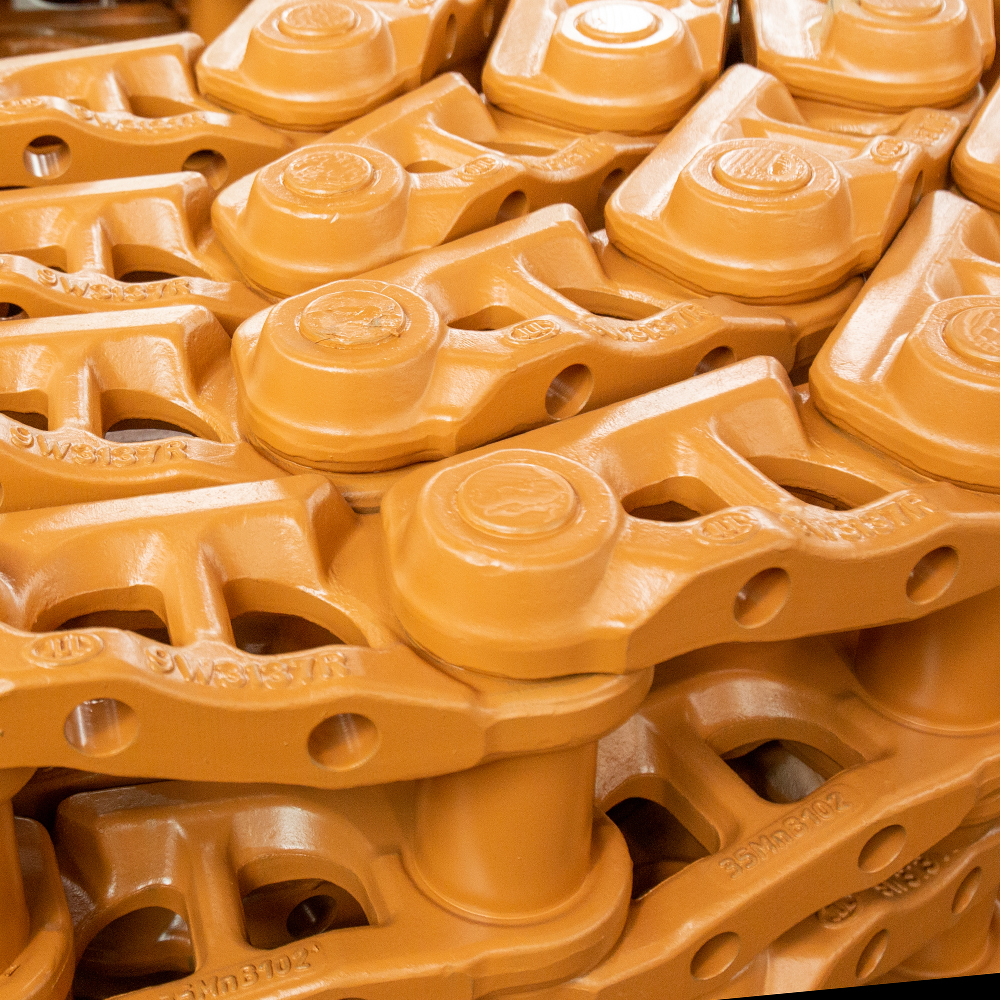